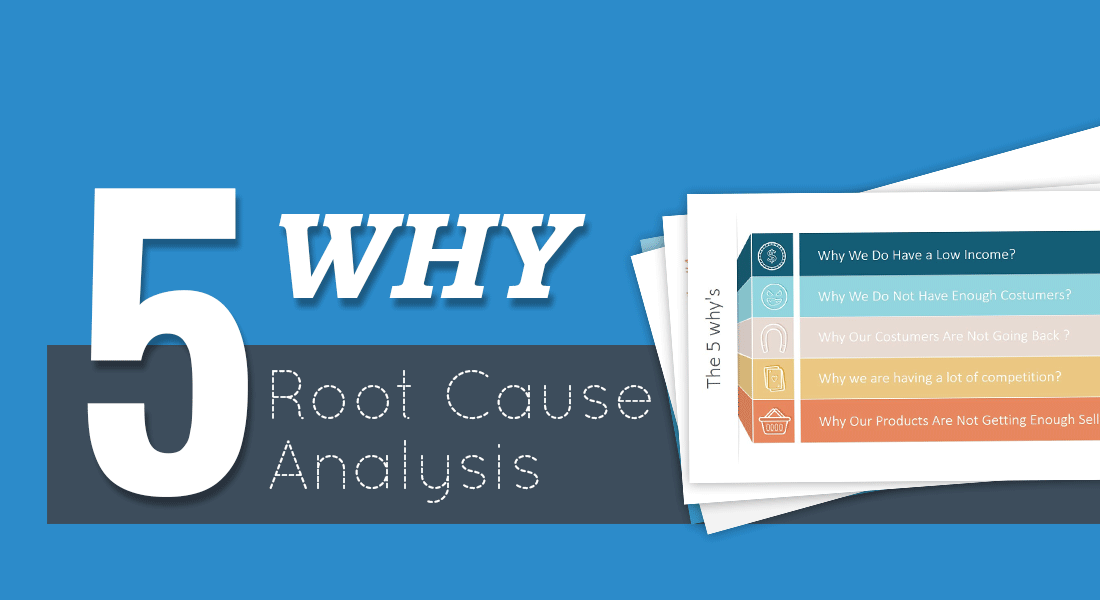
The regular rut of life or the professional wheel, problems can leave you fumbled and dumbstruck at any bend of the road. Mostly unforeseen and uninvited, some problems can have you at your knees while others can bring you to the wits end in an instant. Irrespective of which realm of life you encounter a roadblock, problem-solving is a life-skill to master. It is often seen that people tend to only treat the problems while neglecting the root causes. This is a very common scenario at workplaces.
When it comes to problems that you face within the bounds of your work, there are several tools available today. These can help you solve the problem and circle out the root cause, so that you can prevent it from happening again in the future sometime.
What is Root Cause Analysis?
RCA or Root Cause Analysis is an intelligible and widely-used technique that helps people pinpoint reasons that caused the problem to occur. It makes use of a certain set of steps in association with tools and aims at identifying the origin of the problem. Basically, with root cause analysis you can figure out the ‘whats’ and ‘whys’ of any problem that you face.
Root cause analysis is based on the assumption that events and systems are interrelated in some or the other fashion. It runs on the model where an action is a given area fired off an action in some other area and it goes on like a chain of actions. RCA says that when you start tracing one action at a time, there will be a point where you will be able to point out how the problem started and what caused it to grow into a roadblock.
Now as we’re discussing about Root Cause Analysis, it is important for you to know the different methods or tools available to conduct an RCA analysis, especially if you are going to present this analysis to an audience as an outcome of the problem resolution. As our systems and problems are synchronously evolving so are these RCA tools.
Our focal point for this article will be the 5 Whys method of root cause analysis as it remains the most-effective and reliable one for a wide range of problems.
5 Whys as an Effective Root Cause Analysis Tool
As mentioned above, 5 Whys is one of the most common RCA tools. It is an organized and straightforward method to recognize the underlying cause of a given problem. The process involved delivers great value by driving you to discover the causative, solve the problem and ensure that it does not trouble you again in the future.
Once you get to the base of the problems, it helps you prevent the future instances where you would otherwise end up putting in a lot of time, effort and money.
Putting it out in simple words, the 5 Whys method simply involves asking “Why” until all the symptoms of a problem trace down its root cause. It is often used in combination with other methods like the Cause and Effect Diagram. However, it works equally well when used as a standalone RCA method. It is observed to be seen at its effective-best when the answers are provided by those who have a behind-the-scenes knowledge and experience of the process being examined.
Before tapping further into the subject, let’s walk you through the origin and history of this exemplary tool.
The Origin of 5 Whys
The origin of 5 Whys can be traced back to the soil of Japan. Sakichi Toyoda, the founder of Toyota Industries was the brain behind developing this technique. Developed in 1930, the company is believed to still use this tool for root cause analysis and problem-solving. The technique gained popularity during the 1979s and it is still used by Toyota and other companies and organizations today.
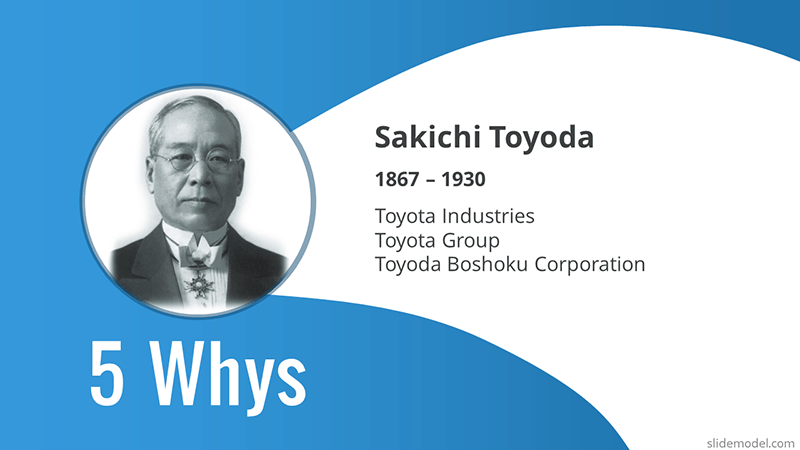
The coining of this technique demonstrates a very unique fact about Toyota itself. And, that is its “go and see” philosophy. Their decision-making is based on the practicalities and not theoretical remarks or assumptions.
Benefits of 5 Whys
We’ve been speaking greatly about the efficiency of this tool but now let’s look at some real back-story on the benefits of using 5 Whys for problem-solving.
Helps Determine the Human Error
An architect at Toyota speculated that behind most technical problems, some of the other human errors leans in.Following is an example that was given to demonstrate the claim.
Following this course, what was originally seen as a technical fault was revealed to be a human lag.
Speeds up the Problem-solving Process
Evident and obvious, this RCA tools speed up the problem-solving process to a great extent. When a problem is recognized accurately, it can be addressed in a proper and organized manner. This helps in solving problem in a relatively shorter duration while making sure that the usual workflow and pace are maintained within a team.
Determines Time Required to Fix a Problem
Not only does 5 Whys acts as a time-saving tool, it also helps in determining the estimated time to fix a problem. When you reach the root cause in a relatively lesser time and identify the solutions, chances are bright that you can measure the required span to deal with the problem.
Minimizes the Chances of Future Problems
Once the root cause of a problem is pointed out, future instances of its occurrence is minimized to a great extent.
Overall, in a functional workspace, 5 Whys can be a simple yet sophisticated method of problem-solving and prevention.
Treading forward, let’s look into the process.
What Does the 5 Whys Process Looks Like?
The process is often subdivided into 4 steps.
Step 1: Come to an Agreement regarding the Problem
Until and unless you define the problem properly, solving it is going to be an uphill task. Spend some time ensuring that you’ve defined the problem really well. The detailed your definition of the problem will be, the easier will be for you to solve it.
Step 2: Shoot the “Whys”
Check one layer at a time and keep shooting a “Why” as soon as you come across a problem at every level.
Step 3: Determine if a Cause is the Actual Root Cause
Every time you come across a cause, stop there and take some time to analyze if that is the root cause or not.
Steps 2 & 3 will have a symbiotic relationship throughout. You may have to repeat these a couple of times before coming to a conclusion about the actual root cause.
Make sure you ask the Why question at least 5 times to get to the root cause.
Step 4: Fix the Cause and Eliminate the Symptom
Fixing the problem alone is not going to give you the real value. Pay attention to fixing the error and the cause so you a prevent any future occurrences of the problem.
Let’s look at an example for you to understand the process in a better light.
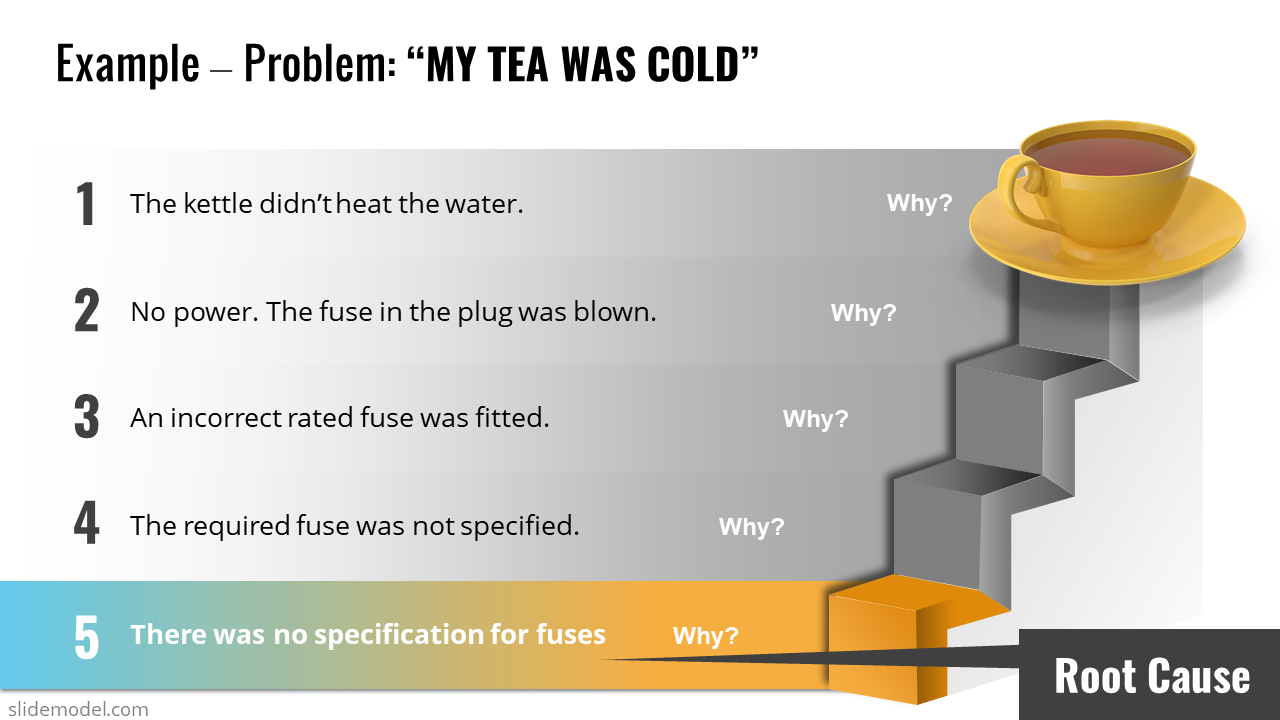
Example of 5-Whys technique presented using Multi-level PowerPoint template
Using PowerPoint Dashboards for Root Cause Analysis
Now that you have an insight into what 5 Whys tool is and how its process flows, it is important that you understand about its presentation.
How you present the analysis solves half of the problem because it makes the flow easy to understand.
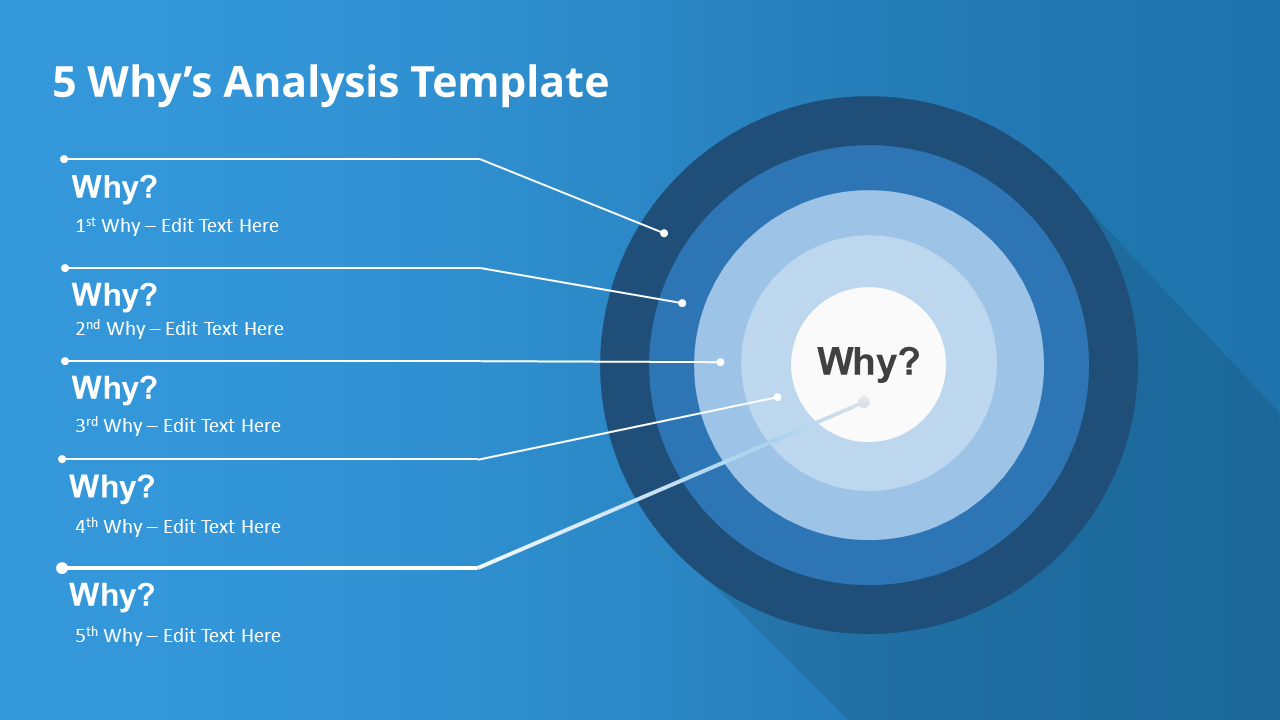
Many professionals are recommending the use of PowerPoint dashboards for the 5 Whys template.
Here’s one dynamic 5 Whys PowerPoint template that you can use.
This one contains a set of three slides.
- The first one is a framework diagram that can be used to present how each dimension was traversed. It also gives an overview of how the next question was chosen.
- The next set of slides contains 5 Horizontal banners. In these, each question of the analysis along with the context of the cause can be presented.
- Third and the last set of slides of this template is used for making the questions more descriptive. Here, the presenter can give a detailed account of the process.
With the help of such templates, an iterative process such as the 5 Whys Root Cause Analysis can be explained and demonstrated seamlessly.
The real value of the time that you spend undertaking such a Root Cause Analysis can only be redeemed when your presentation falls in the right spot.
Recommended article: 23 PowerPoint Presentation Tips
We have seen how the Five Whys technique can be used as a process to understand any problem. If the 5 Whys technique is not the type of RCA that you need, there are others that you can use. Nowadays, there are different Root Cause Analysis PowerPoint templates available. So demonstration is not something you need to fret about!
Very resourceful and useful to all industries including Oil&Gas , Transportation and Human Physical and Health related problems.